Wright C+
Conserve Plus
Total Resurfacing with the CONSERVE® PLUS Implant
Unlike a total hip replacement, total hip resurfacing allows the patient’s femoral head and neck to be retained and the patient’s femoral canal is not invaded. This procedure helps preserve the patient's bone, as well as, natural motion in the joint.
Wright’s large femoral head components enable the CONSERVE® PLUS Total Resurfacing Implant to offer a hip procedure with excellent stability and range of motion. Many patients with total resurfacing implants enjoy a pain-free life with increased activity levels for many years.
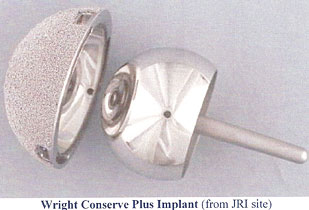
Implant utilizes the same BFH® Technology as the CONSERVE® Total Hip Implant. Thus, the same benefits of large diameter metal-on-metal bearings are maintained. BFH® Technology has produced a superior artificial hip that is more like your normal hip anatomy in size and function
What components make up total resurfacing implants?
CONSERVE® PLUS Acetabular Shell and Femoral Head
The CONSERVE® PLUS acetabular component is a super-finished cobalt chrome shell manufactured to the tightest tolerances in the orthopaedic industry. The acetabular component is a "low profile" component, which allows for an additional 10º range of motion compared to "standard profile" shells. This acetabular component mates with a super-finished cobalt chrome CONSERVE® femoral head for excellent metal-on-metal implant longevity. These two components form an extremely stable hip joint because of the size of the femoral heads, which range from 36-56mm in diameter (compared to traditional 28mm heads). The CONSERVE® Family of Implants is designed with BFH® Technology (large femoral heads) which allows for a range of motion up to 172°. This is significantly better than many standard total hip devices which fall into the range of 130° - 135°.*

A key advantage to the increased range of motion offered by the CONSERVE® PLUS resurfacing implant is the reduced chance for dislocation. Remember, hip dislocation is one of the leading causes for failure of a total hip replacement and is a strong advantage of hip resurfacing – almost no dislocations!!
Photo: CONSERVE® PLUS Acetabular Compound X-ray
CONSERVE® PLUS Implant Design
The CONSERVE® PLUS Implant utilizes the same BFH® Technology as the CONSERVE® Total Hip Implant. Thus, the same benefits of large diameter metal-on-metal bearings are maintained. BFH® Technology has produced a superior artificial hip that is more like your normal hip anatomy in size and function. In traditional hip surgery, the diseased hip is replaced with a joint that is much smaller in size which can make the new joint susceptible to dislocation. In contrast, the larger femoral head in the BFH® Technology Hip reduces the chance of post-operative dislocation while increasing the range of motion. In fact, BFH® Technology allows patients to potentially achieve up to a 172° range of motion, compared to 130° - 135° of Wright’s traditional implants.* This extra range of motion can make a big difference for those trying to return to a normal, active life.
Advantages
You do not have to live with hip pain for the rest of your life. Total hip resurfacing is one alternative that can help reduce pain in your joints. Pain relief is the most reliable potential benefit of resurfacing and often the major reason for surgery. For most people, hip resurfacing surgery also offers better movement, strength, and coordination of the torso and leg.
Another benefit is an improvement in the appearance of the limb. Most people who develop a limp in order to cope with the pain of an arthritic condition will no longer limp after surgery. Hip resurfacing surgery may mean the difference between having to use a walker or cane and being able to walk, climb stairs, and maintain a relatively active and independent life.
The CONSERVE® PLUS Total Hip implant is a wonderful option to total hip replacement. The design goals include:
- Bone stock conservation and preservation
- Biological bone preservation and normal joint physiology
- Improved stability
- Minimal morbidity (disability)
- Revisability
These advantages have been cited by Dr. Harlan Amstutz in the abstract "Advantages of Metal-on-Metal Hybrid Resurfacing (CONSERVE® PLUS Implant)", which he presented in January 2004. Dr. Amstutz is the recognized world leader in total resurfacing arthroplasty.
Only you and your orthopaedic surgeon can make the decision about how to deal with your hip pain. Total hip resurfacing can improve your quality of life and allow you to return to your daily tasks and low-impact activities with greater comfort. Call your orthopaedic surgeon today to see if you are a candidate for the CONSERVE® PLUS implant.
Study Results
Following the reintroduction of metal-on-metal articulating surfaces for total hip arthroplasty in Europe in 1988, Wright Medical developed a surface arthroplasty prosthetic system using a metal-on-metal articulation. The present study describes the clinical and radiographic results of the first 400 hips treated with metal-on-metal hybrid surface arthroplasties at an average follow-up of three and a half years.
The studies highlighted in this section validate Wright's commitment to our customers and the patients they serve. Wright is committed to the continual improvement in the wear and functional performance of metal-on-metal hip bearings through design, material and production process optimization.
Metal-on-Metal Hybrid Surface Arthroplasty: Two to Six-Year Follow-up Study (MH015-104)
By Harlan C. Amstutz, MD, Paul E. Beaule, MD, FRCSC, Frederick J. Dorey, PhD, Michel J. Le Duff, MA, Pat A. Campbell, PhD, and Thomas A. Gruen, MS
CONSERVE® PLUS Metal-on-Metal Frequently Asked Questions
1.) How long has metal-on-metal articulation been in use?
George McKee of Norwich, England, was the first to use metal-on-metal articulation with modified Thompson stems and a one-piece cobalt chrome socket combination in THR in 1953. The design was primitive, but many lasted for more than 14 years. In 1986, August et al. reviewed 657 total hip arthroplasties performed by McKee and Farrar. The combined survival rate of the hip and stem at fourteen years was 84.3%. Loosening was cited as the main cause of failure, and bone cement was cited as the main culprit. The authors never implicated metal-on-metal articulation as a reason for complications in their paper.5 Although metal wear was detected in devices that were revised, McKee did not observe any undesirable effects of that debris on the soft tissues or the bone.6 The early history of metal-on-metal devices, including Dr. Amstutz ' experience with the McKee device in New York, has been previously published.7-9
2.) What is the optimum material for metal-on-metal articulation?
Metal-on-metal articulation is typically associated with the cobalt chromium molybdenum alloy. These alloys are divided into two categories: high carbon, where the carbon content is above 0.20%; and low carbon, where the carbon content is less than 0.05%. Several studies comparing both groups have been conducted. Earlier studies presented inconclusive results.10 By comparison, later studies isolated the contribution of factors such as surface finish, clearance, sphericity and carbon content. There is now general consensus in the industry that the high carbon alloy has much better wear resistance than the low carbon type.11
In addition, there are two types of processes used in manufacturing the cobalt chrome molybdenum components. One method is casting the components (used by Wright for the CONSERVE® PLUS and CONSERVE® Total implants). The other is forging the material. Although the chemical composition can be exactly the same between the two materials, there is a structural difference. The grain size of the forged alloy is typically less than 10 microns, whereas the grain size for the cast material ranges from 30 to 1000 microns. There is also a marked difference in the appearance of the carbides, in that the carbide regions tend to be smaller in the forged material. Metal liners and femoral heads have been produced at Wright with both types of material. A limited number of couples were tested in a hip wear simulator. The test showed less wear with cast high carbon alloy than the forged alloy. Due to the limited number of samples, the difference had low statistical reliability.11 This study was the basis for Wright’s decision to use cast cobalt chrome alloy as the material of choice for their metal-on-metal components.
3.) Does the clearance between articulating components play a role in wear debris generation?
Absolutely! This is probably the most influential factor in wear behavior. The proper clearance is essential for entrapping the synovial fluid between the articulating surfaces. This fluid is largely responsible for separating the surfaces while the joint is in motion, thereby reducing wear. If the gap between components is too small or too large, there is a sharp increase in wear rates.12 A study conducted by Isaac, Dowson and others (DePuy International, Leeds, UK) compared wrought and as-cast components with various clearances between those two groups. The results of the hip simulator study strongly indicated that clearance plays a major role in wear rates and that "wear appears to be relatively insensitive to changes in materials that have similar chemical compositions but different microstructures."20
4.) Does the CONSERVE® PLUS acetabular shell with the big femoral head use the same clearance for all sizes?
No. The clearance between components is size-dependent. The larger the diameter, the larger the gap between the components. The range for the entire family of sizes is from 90 to 200 microns of diametral clearance, each bearing size having an optimized gap for maximum fluid film thickness.
5.) I've heard a lot about heat-treated cobalt chrome components versus "as cast" components. What are they talking about and is there a difference?
Cobalt Chrome Molybdenum components that are cast usually go through the hot isostatic pressing (HIP) and solution annealing processes to remove microporosities often found in castings and to improve the ductility and homogeneity of the material. The microstructure of this type of heat-treated material looks different from that of the original casting. It is important to note that even though heat-treated material looks different, it doesn’t affect wear. Two global metal-on-metal resurfacing manufacturers use the heat-treated process for the castings (Corin, LTD. and Wright). Midland Medical, the producer of the Birmingham Hip Resurfacing (BHR) implant, leaves the castings untreated. The BHR product champion, Derek McMinn, MD, claims that heat treatment can lead to carbide depletion, which can adversely affect wear rates. One "pin on disk" type test suggests that "as cast" material wears slightly less than "HIP" cast material; however, the data shows so much scatter that the results are inconclusive.15 In addition, the linear tracking motion of the type of "pin-on-disk" used in that study is very different from the actual hip motion. A linear tracking pin-on-disk test is conducted by sliding the cylinder on the flat surface back and forth along one axis. The actual movement of the femoral head inside the socket produces crossing path motion. Studies in hip simulators are more relevant since they more closely resemble the actual hip function by reproducing this crossing path motion. It has been shown that a linear tracking pin-on-disk test under-estimates UHMWPE wear rates by 10 to 100 times, and overestimates metal-on-metal wear rates as compared to hip simulators and retrieval studies.17 Midland Medical has not published any data from a hip simulator to support their claim. Also, zero clinical studies have been conducted which suggest BHR components create less wear than heat treated components.
Bowsher et al. conducted a hip simulator wear study in which 40mm diameter metal-on-metal bearings, either "as cast" or heat treated, were compared side-by-side.13 Wear rates were compared for the running-in state (first 1 million cycles), steady state, and also fast jogging. In all three conditions, there was no difference between wear rates of the two forms of the alloy. The authors concluded that HIPing and solution annealing do not adversely affect the wear rates of large diameter metal-on-metal articulations. Furthermore, one additional study was presented at the recent June 2003 Conference on Metal-on-Metal Devices in Montreal that corroborate the Bowsher study.20
6.) What is the "steady-state" wear?
Typically, metal-on-metal couples in the hip simulators go through the "run-in" or "wear-in" period where the weight loss due to wear increases linearly. At some point, usually between 500,000 and 1 million cycles, the wear increase drops dramatically or stops altogether. It is then said that the metal-on-metal couple reached the "steady-state" of wear.
7.) Does the surface finish affect wear rates?
Surface finish has a definite effect on wear rates. The rougher the surface finish, the higher the peaks of material that eventually will be removed. Typical surface finish for the CONSERVE® resurfacing components is 0.008 microns (micrometers). This is an order-of-magnitude smoother than the finish on typical metal femoral heads articulating with polyethylene inserts used for THR.
8.) Do larger heads wear less than smaller heads?
Theoretically, if the metal couple is dry, larger heads should wear more than smaller heads due to their longer sliding distance per step. However, in the presence of the fluid the opposite is true: larger diameter heads should wear less because of their greater sliding velocity. Calculations show that larger diameter wear couples can form a thicker synovial fluid film between components.12
H
H
D is the head diameter
Ú is the entraining velocity
According to the formula above, the larger the articulating diameter, the larger the Hmin value. A thicker fluid film means less contact between hard surfaces during motion and, presumably, less wear. Does this theory prove itself? The study cited above compared 22mm, 26mm and 35mm diameter metal-on-metal articulations and found no difference between the three. Isaac compared 16mm, 22mm, 28mm, 36mm and 54.5mm diameter couples and, for diameters 28mm and larger, it was determined that wear decreases with increasing head diameter.20
In the study of the 54mm articulating couple conducted at Wright, the wear rates were found to be very similar to the wear rates for the 44mm CONSERVE® PLUS articulating couple performed at another institution. These numbers are in agreement with other experimental data obtained with hip simulators.
9.) What do they mean when they say that cobalt chrome is "self-healing"?
A cobalt chrome articulation has the ability to polish out the scratches from abrasive damage such as third-body wear. In retrieval studies, the deep scratches have often been partially or entirely polished out of the main contact zones.
10.) What is the average particle size for metal wear debris?
In one study, the cobalt chrome particles from a McKee-Farrar metal-on-metal articulation were in the range of 6 to 744 nm (nanometers), with an average size of 42 nm.16 By comparison, polyethylene particles range from 0.05 to 5 micrometers (50 to 5000 nm).
11.) Can a metal-on-metal articulation prevent osteolysis?
Since a metal-on-metal articulation does not eliminate wear entirely, there is always the potential for an osteolytic reaction. There are reports of isolated cases of osteolysis with metal-on-metal joints.17However, these are mostly limited to the first-generation metal-on-metal components. Those were implanted with acrylic cement, which can fragment and generate third-body abrasive particles. It is believed that the metal debris is too small, in comparison to the polyethylene particles, to initiate an osteolytic reaction. A study of several metal-on-metal components (Metasul ™ total hip replacements and McMinn surface replacements) investigated the bone and tissue reactions to the metal debris.18 It was noted that metallosis (a grey-black appearance of the soft tissue) was present with the surface replacements and the total hip replacements. Macrophages filled with metallic particles were found in all tissues, but in larger amounts in those with metallosis. Giant cells and small areas of histiocytic granulomas were also present. The authors noted that there were fewer macrophages and giant cells than typically seen in tissues around metal-polyethylene joints, and although an inflammatory response to the metal particles was present, this was not as severe as the response to the cement particles. The authors concluded that the long-term response to these very small CoCr particles should be monitored. There has been no observed occurrence of metallosis in connection with CONSERVE® PLUS or CONSERVE® Total implants.
CONCLUSIONS:
Many factors affect metal-on-metal wear behavior. Some of them are more significant than others. Surface finish, appropriate radial clearance and high carbon content have been shown to play the greatest role in reducing wear rates.
The microstructure of the alloy does not play a key role in wear behavior. "As cast" and heat treated alloys were directly compared in hip simulators by the scientists from Corin, DePuy, Centerpulse, and in some independent laboratories, all showing similar wear rates for both types of alloy. Proponents of "no heat treatment" regimes have not provided us with laboratory or clinical data to date. McMinn’s claim of better metallurgy with the "as cast" components is based primarily on "pin-on-disk" type testing. The "pin-on-plate" or "pin-on-disk" type experiment can compare the wear of different materials as a flat surface, but the mechanism of these tests has nothing in common with the motion of the hip joint.
Hip simulators offer the most reliable way to assess wear in the laboratory, but keep in mind that the outcome greatly depends on the method, testing equipment, and measuring equipment. Since we are dealing with tiny amounts of debris, test results may vary greatly from one hip simulator study to another. Take that into account when comparing data between two tests conducted by different people and with different equipment.
Finally, the best proof of a good design is in the clinical outcome. The CONSERVE® PLUS metal-on-metal articulation has a good clinical history with over 6 years and over 1300 patients. The paper presenting the clinical results of the first 400 CONSERVE® PLUS hip resurfacing cases performed at the JRI has been accepted for publication by the Journal of Bone and Joint Surgery.